Research Themes
Material Development Tailored with Optimum Process Parameters
While tremendous progress has been made in additive manufacturing over the past 30 years, the focus of new materials and technologies has been on polymeric materials. However, the demand for metallic parts made using AM processes exceeds that of polymeric materials within the global manufacturing sector. The global AM sector has consistently focused on using highly engineered powders which are exceptionally expensive and constitutes a significant portion of the final part cost; on average, 20%. The significantly higher net cost of metallic parts made by AM is a key factor inhibiting market growth. As the result of the powder grade constraints, only a limited number of metals or metal alloys are presently being used in commercial metal additive manufacturing. For AM metal parts to be a viable option for industry, new, high quality reproducible powders with characteristics that are appropriate for AM processes and applications must be developed. HI-AM’s research in Theme 1 will contribute valuable new metal powder options and it will increase processes reliability and repeatability rate by creating dynamic process maps to control the final quality and material properties of the finished part.

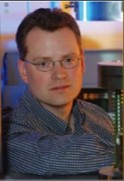
Theme Leader
Paul Bishop, PhD, PEng
Dalhousie University
Dept. of Mechanical Engineering
Email: Paul.Bishop@dal.ca
The objective of this project is to generate new powder metal feedstocks, with compositions strategically chosen to have a widespread and immediate impact on the global AM community. These new materials will broaden the mechanical, physical, and corrosion properties attainable within metallic products. This will help position AM as a viable manufacturing approach for a greater number of industrial applications.
Aluminum is an attractive option for AM because of its low inherent density, high strength to weight ratio, and its corrosion resistance. Al is a high value commodity in Canada and developing new Al alloys for AM is a direction that will positively impact national economic growth. This work will concentrate on two key challenges: 1) solidification cracking, and 2) chemistry changes via element evaporation. The research will focus on alloys with chemistries devoid of elements prone to volatilization during laser processing, (i.e. Zn, Mg, etc.) and low melting point eutectics, with consideration of solidification conditions and the strengthening mechanism targeted (heat treatment, dispersoids, or solid solution strengthening).
Principal Investigators:
![]() Paul Bishop |
![]() Mathieu Brochu |
![]() Hani Henein |
Titanium and its alloys represent a material category of major importance to the global aerospace sector, as it is a lightweight metal with significantly greater strength than most aluminum alloys. The objective of this subproject is to design and process innovative Ti alloy powders via LPF- and LPB-AM to expedite the adoption rate of these alloys within AM. The initial focus of this research is LPF-AM. Here, any new Ti-based powder systems must be designed to (1) impart attractive metallurgical attributes (i.e. mechanical properties, microstructure, corrosion resistance, etc.) within the finished products and (2) facilitate the manufacture of products that are dimensionally accurate, sound, and cost-effective.
Principal Investigators:
![]() Paul Bishop |
The use of AM for the fabrication of geometrically complex tools and dies is ideal, as the production volumes are low, geometries are complex, and the materials used in fabrication are challenging to process and machine within the confines of conventional forming technologies. The bulk of commercialized activities in this area have been constrained to H13 tool steel. The objective of this sub-project is to investigate the AM of alternate tool steels that embody similar metallurgical traits to H13 as well as other strategic benefits in terms of resistance to wear (grade A8) and shock loading (grade S7) in order to enable AM to be implemented in much wider range of tooling applications. Furthermore, Sc additions have been proposed to offer dramatic increases in strength to Al-Si alloys. Of interest is the increased strength that can be derived from hypoeutectic Al-Si-Sc alloys. The objective of this part of the sub-project is to explore the increases in strength achievable through the rapid solidification of an Al-10Si-0.4 Sc alloy. An additional objective of this sub-project is to characterize 17-4 precipitation hardened stainless steel, which is widely used in numerous fields, such as the aerospace, chemical, and mining industries as well as NiCrBSi or NiBSi with WC composites used in the oil sands and mining industries for wear applications.
Principal Investigators:
![]() Carl Blais |
![]() Hani Henein |
Most studies in nickel alloys have emphasized alloys 625 and 718, as they represent common workhorse alloys within the fabrication of gas turbine engines. Canadian companies operating in this sector are keen to implement these alloys as well as IN939, IN100, and Hastelloy X within the confines of AM. The goal of this subproject is to identify new nickel-based alloys and to find strategies to reduce the detrimental effects of the low melting point phases or reactions that prevent the fabrication of defect-free parts.
Furthermore, the fundamental conditions in which intermetallic materials can be processed by LPBF is studied in this project as well. The knowledge on AM of intermetallics is almost inexistent in the literature. This category of materials has a significant portion of its atomic bonding being covalent in nature, which increase its strength and reduces the ductility. As such, these alloys are less compatible with the thermal cycles imposed during AM. To that extend, the relation between intermetallic alloy and its cracking behavior during rapid thermal cycling is investigated from fundamental principles. Elucidating the paradigms would possibly open processing strategies for these alloys. The alloys investigated includes Ni-aluminide, Ti-aluminide and Fe-aluminide.
Principal Investigators:
![]() Mathieu Brochu |
![]() Kevin Plucknett |
In this sub-project, the use of molybdenum alloys in LPB-AM will be investigated. Such alloys are of significant interest to aerospace engine manufacturers as a viable alternative to aluminide systems, yet little is known about their suitability for AM processing. Research will emphasize fundamental studies wherein solidification maps and the conditions (G and R) needed to achieve high-density products will be elucidated.
Principal Investigators:
![]() Mathieu Brochu |
Everyday composite materials are becoming lighter and stronger due to stringent industry standards such as CAFÉ 2025. As a result, lightweight, high strength composite structures are being used in many scenarios, ranging from small-scale biomedical industries to large-scale aerospace and tooling sectors. Lightweight materials are conventionally developed through micro-scale modifications, foaming, and by macroscopic material structuring. Functional grading of materials and foams are two of the more common practices for reducing material weight and commonly occur with the use of conventional subtractive manufacturing. However, it has been proven that customized multi-material objects with a complex internal architecture can easily be created through AM using lightweight, functionally graded polymer materials. Project 1.2 will build on this knowledge to investigate the use of metallic powder feedstocks in the same context, when utilizing BJ- and LPF-AM processes. At present, these AM technologies have not been utilized for such applications, due to challenges in binding different metallic materials together, difficulties in feeding different types of metals into AM systems, problems in controlling print resolution, and the collapse of the thin walls associated with porous structures during printing.
The objective of this sub-project to strengthen the Canadian knowledge on the development of metallic FGMs using LPF-AM. To this end, the research team is developing and optimizing the microstructure of filler materials and their corresponding binders for BJ-AM of novel composites.
Principal Investigators:
![]() Hani Naguib |
To successfully develop FGM products, the sensitivity to processing parameters must be established in order to identify the processing window required to achieve the desired properties. The sub-project outcome will be a process map that correlates alloy chemistry, solidification/cooling temporal conditions and non-equilibrium microstructures under process/phase content maps. It will contribute to the databases required for the development of multi-material parts using LPF.The research results of this subproject will have tremendous utility in the tooling industry where the requirements include: high thermal conductivity materials for rapid cooling, as well as abrasion and impact resistance.
Principal Investigators:
![]() Kevin Plucknett |
Metal alloy powder costs are principally driven by two factors. One is the frequent use of rather exotic, non-conventional fabrication routes that produce particles of an exceptional quality, but at relatively low production rates. The second factor is that most powder production processes generate particles that follow a log-normal size distribution. Since their standard deviation typically falls between 2.0 and 3.0, yield becomes a significant problem given the restraint that only a narrow cut of powders is selectively extracted for current AM operations. Hence, it is not surprising that the metal powder costs will be the largest continuous expense through the life of an AM machine. Therefore, industry is very interested in concepts that have the potential to reduce raw material costs. Although adoption of AM technologies will most likely lead to a decrease in raw material costs through economies of scale, strategies must be devised to reduce material costs and/or maximize their utilization. Such developments are particularly important in the near term as it is expected that a growing number of new materials designed specifically for AM will soon become commercially available (i.e. Nanosteel BLDRmetal J-10, Airbus Group Scalmalloy, Alcoa $60M additive manufacturing center, etc.).
The objective of this sub-project is to understand the printing environment and to characterize the effect of recycling unfused particles in consecutive builds with/without additions of various volume fractions of new (unused) particles. The framework will be developed around a Ti-based alloy given the intense use of this metal in AM, and its acute sensitivity to changing levels of impurities (i.e. O, H, N, C).
Principal Investigators:
![]() Mathieu Brochu |
![]() Gisele Azimi |
Current powders used in LPB-AM are required to be nominally spherical, and are created using gas or plasma atomization. Powders with irregularly-shaped particles can be produced at a much lower cost than the spherical ones (i.e. water atomization, hydride/de-hydride, Krolle processes etc.). In this sub-project, transforming the irregular low cost alloys to spherical particles is being studied.
Principal Investigators:
![]() Carl Blais |
Alloyed and tool steel powders are typically utilized in AM to create tooling for conventional material forming technologies. Such parts are produced in very low volumes as they can endure long periods of use and have a complex geometry that is only suitable for the production of a single product design. Studies show that AM parts produced from water-atomized low-alloyed steel powders have similar mechanical properties to those obtained with gas atomized powders. The objective of this sub-project is to build upon these prior investigations to determine the effectiveness of using low-cost atomization techniques as a means of powder production of other alloyed and tool steels.
Principal Investigators:
![]() Carl Blais |
![]() Paul Bishop |
![]() Hani Henein |