Keynote Speakers

Anthony Rollett
US Steel Professor of Metallurgical Engineering and Materials Science
Carnegie Mellon University, PA, United States
Rollett is the US Steel Professor in Metallurgical Engineering and Materials Science at Carnegie Mellon University where he has been since 1995, having previously been at the Los Alamos National Laboratory from 1979. He is recipient of multiple awards including Fellow of TMS in 2011 and International Francqui Professor for 2021-2022 (Belgium). He is known for his work on texture, 3D microstructures and micromechanical simulation. He is a co-Director of the NextManufacturing Center at CMU and is a leader in research & education in metals additive manufacturing.
Rapid advances in 3D printing of metals have enabled widespread used in industry. Key questions remain as to how to qualify printers and certify parts, especially in terms of defect structures. Under support from the NASA-ULI program, a multi-university team is determining process windows, characterizing defect structures, microstructures & surface finish, and measuring fatigue resistance in 4-point bend fatigue. Preliminary results point to similar process windows for the same model at different locations when using a consistent source of Ti-6Al-4V powder. Microstructure and basic mechanical properties can be predicted from thermal history albeit heuristically. Transferring the methodology to an aluminum alloy in a different printer, however, required re-evaluation of melt pool sizes, which is basic to the proposed physics-based approach to qualification. The fatigue results reveal a strong dependence of life on defect content, as expected, which suggests a close connection to the process window for printing. Overall ICME needs include the need for computational tools that predict melt pool shape & size, melt pool stability, microstructure formation, including texture, diffusion, and solid state phase transformation. The ultimate aim is to predict the process window for a given material and printer.

Simon Hoeges
Director Technology & Manufacturing Engineering
GKN Additive, Germany
Simon is responsible for Technology and Manufacturing Engineering at GKN Additive. He joined GKN in 2014 after positions in Medical industry and Academia all associated with Additive Manufacturing giving a track record of 15 years within the technology. At GKN he is responsible for development, validation and global implementation of new technologies, processes and materials. The technology focus within GKN Additive is with Laser Powder Bed Fusion and Binder Jetting showing strong synergies with its parent company GKN Powder Metallurgy. Simon holds a diploma in physics and a PhD in mechanical engineering from RWTH Aachen University.
Abstract: Currently early adopters of AM technology are struggling to cross the chasm to wider application industrialization. The main limitations of AM being design know-how at the end users, production throughput, industrialization / automatization limitations and material variety / properties. Although Additive Manufacturing is evolving from the Advanced Manufacturing industry since several decades there is still a low number of available materials designed to utilize the full strength of the technology. Standard casting, forging or sheet metal materials are applied even though the properties could be significantly enhanced by adopting material chemistry and processing parameters to the application requirements and technology boundary conditions. It is now time to develop and validate in line with promising serial applications tailored materials and production processes. This keynote gives an overview and examples on materials developed for Laser Powder Bed Fusion and Binder Jetting technology applied to produce serial parts in the automotive and general industry.
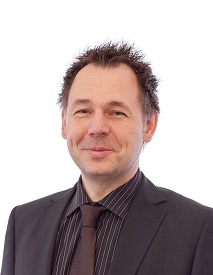
Michael Schmidt
Head of Institute of Photonic Technologies
Friedrich–Alexander University Erlangen–Nürnberg, Germany
Since 03/2009 Head of Institute (Ordinarius), Lehrstuhl für Photonische Technologien, Friedrich-Alexander-Universität Erlangen-Nürnberg
Since 01/2005 Managing Director, Bayerisches Laserzentrum GmbH (blz)
Mega Grant (Presidential Grant) in Russia: Build up a laboratory on Additive Technology with KAI - Kazan University (2014 – 2018)
INO - Institute National d’Optique, Québec, Canada: Associate Researcher (2011 - now), Member of R&D Advisory Committee (2011 - now)
Laser Demonstration Center (LDC), Sankt Petersburg: Advisory Board (2009 - now)
CIRP: STC-E-Chairman (2020 - 2023) ; Associate Member (2014 – now)
Abstract: Recent advancements in laser- and powder-based Additive Manufacturing (AM), individual AM processes have raised interest in science and industry. Especially, powder bed fusion with laser beam (PBF-LB/M) and direct energy deposition (DED-LB/M) have revolutionized today's research and development. These technologies offer the potential to modify an existing alloy by adding specific micro or nano-scale powders to the initial host powder. By using in-situ alloying strategies both chemical composition and microstructural properties can be adjusted which enables producing materials with innovative and outstanding characteristics. Herein we present the benefit of adding nanoscale additives to the initial host powder for two different alloys. Firstly, we investigated the influence of titanium boride (TiB2) nanoparticles (NP) on the processability of the hot crack-sensitive aluminium alloy EN AW-2024 in PBF-LB/M in detail. The focus here is on the impact of TiB2-NP on the process window for the generation of nearly-fully dense and crack-free specimens. The second part is devoted to the processing of NP reinforced hot-work tool steel powder (1.2343) in DED-LB/M. The aim of these investigations is to identify and to understand the effect of carbon, tungsten carbide and TiB2-NP on residual austenite content, the crystallite size of martensite and austenite and mechanical properties.
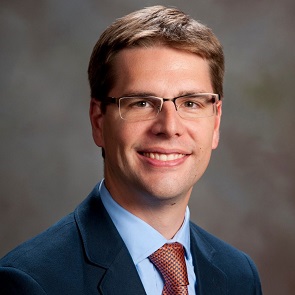
Christopher Williams
Professor, Mechanical Engineering
Virginia Tech, VA, United States
Dr. Christopher Williams is the L.S. Randolph Professor and the Electro-Mechanical Corporation Senior Faculty Fellow in the Department of Mechanical Engineering at Virginia Tech. He is the Director of the Design, Research, and Education for Additive Manufacturing Systems (DREAMS) Laboratory. The lab has published over 185 peer-reviewed articles on topics spanning innovations in additive manufacturing processes and materials, Design for Additive Manufacturing methodologies, and cyber-physical security for AM. He is a recipient of a National Science Foundation CAREER Award (2013). He currently serves as the Vice Chair of the Additive Manufacturing Community Advisors for SME.
Abstract: Binder Jetting is a unique Additive Manufacturing modality as it presents opportunities to print powdered materials that are not processable on other AM platforms. Its use of ink jetting technology provides a pathway to readily scalable manufacturing platform and voxel-level control over material composition. Furthermore, its material flexibility provides pathways for both direct and indirect (e.g., printed tooling) manufacturing routes. In his talk, Dr. Williams will highlight the flexibility of the binder jetting platform by demonstrating examples of processing a series of novel materials systems to realize compositions and products that could not be fabricated by any other route. Examples will include processing of (i) fine copper powders for enhanced mechanical and electrical properties, (ii) jetted nanosuspensions for altered microstructure, (iii) foaming powders to achieve hierarchical porosity, and (iv) foundry sand for fabricating large scale metal-ceramic composite lattice structures.
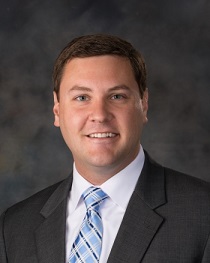